Installation Instructions
WARNING: Electric Shock Could Occur If Used On Wet Surfaces. INSTALLING AT EXISTING OR NEW HOME. | ||
STEP 1: Installing Inlet Valves Wall Valves in Existing Structure
Select as closely as possible the desired location of inlet valve. Drill a small pilot hole in the floor directly below the proposed valve location. A straight length of coat hanger wire, cut at an angle, makes a good pilot hole drill bit, but be careful not to snag carpeting. Leave straightened length of coat hanger wire through/in this pilot hole to serve as locator and guide point. (Fig.3) | From beneath the floor, measure from the pilot hole to locate the center of the sole plate. Note: You may want to drill a 3/4” inspection hold to avoid drilling into bottom of a stud or other “inner wall” obstruction. Drill a 2 1/4” diameter hole through the center of the sole plate. Using a flashlight or probe, inspect interior of wall to be sure there are no obstructions. Note: the opening you re going to cut in the wall for the inlet valve should be located between studs, clear of obstructions such as plumbing, wiring, heat ducts, etc. Minimum stud width for sufficient clearance for inner wall mounting bracket assembly is 2 3/4”. (Fig. 3) | |
Centred approx. 30” above floor level cut an almost square opening 2 3/8” wide by 2” high in the wall directly above the 2 1/4” sole plate hole. Cut or file two 1” high triangular pieces above and below the almost square opening so that your wall opening exactly resembles. (Fig.4) | ![]() | |
![]() | Now cut or break off “New Construction” section from metal wall mounting bracket and glue a sharp 90° elbow to the pre-riveted adaptor ring. (Fig.5) Insert top screw only through inlet valve and gently squeeze inlet valve stem into bracket assembly until you are able to just start top screw threads in bracket assembly hole.
| |
Strip the low volt wire and tape it to sharp 90° elbow with approx. 6” sticking through wire guide hole. Join to inlet valve wires with wire connectors supplied. Attach a small weight to the other of low volt wire and drop weighted wire through opening in wall. Allow wire and weight to hang through sole plate. (Fig. 6) | ![]() | |
Insert assembled 90° sharp elbow and wall bracket assembly through wall cutout hole as illustrated. (Fig. 7) Once metal mounting bracket is completely inside wall cavity, slide entire assembly upwards so metal plate is flush with inner wall surface and inlet valve is flush with outer wall surface. You can insert index finger through wall inlet valve opening and gently squeeze inlet valve stem further into inner wall assembly. (Fig.8) Now insert and partially tighten bottom inlet valve screw. Tuck low voltage wires and connectors under sides of wall inlet valve. Adjust inlet valve for perfect vertical alignment and tighten both inlet valve-mounting screws. Be sure inlet valve lid operates freely. Note: Mount inlet valves lid pulls down to open.
| ![]() | |
Floor Valves in Existing StructureTo install a floor inlet, drill a pilot hole with a coat hanger and check the location as previously described. When you are sure that the proposed location will not be blocked by a joist or other obstruction, cut a hole in the carpet slightly larger than your 2 1/4” drill bit. Drill a 2 1/4” hole in the floor. Chisel or saw this hole larger to accommodate the inlet valve low volt connections. (Fig.9) |
Assemble an Adapter Reducer Bushing and some low voltage wire to an inlet valve. Screw the valve to the floor. Repeat until all inlets are installed. (Fig.10) | |
![]() | Closet Wall Installation — Existing StructureOften it is only practical to install your system with the line coming through the floor inside a closer and then though both sides of the wall. To use this method, select suitable inlet valve location, exercising same precautions as for normal wall installation. Using a length of a coat hanger, pierce a hole through both walls. (Fig.11) Be sure to hold wire perfectly horizontal so that both interior and exterior holes line up with one another. Check for inner wall obstructions by bending the short length of a coat hanger wire at a right angle and twirling this right angle piece inside the wall. Drill a 2 1/4” hole horizontally through both sides of wall. Make the hole in the exterior wall surface into the same shape opening as described previously in STEP 1—(installing inlet valves). (Fig.4) | |
From inside the closet cut a 2 1/4” hole through floor, either directly below an opening in the wall or another convenient spot. (Caution: Make pilot hole as in STEP 1 previously). Run low voltage wire through the 2 1/4” hole in the floor and through the wall to exterior closet. Pass low voltage wire through the wire guide hole of the Inner Wall Closet Assembly. (Fig.12) | ![]() | |
![]() | Tape low voltage wire to this assembly immediately behind the metal bracket. Attach wires to low voltage terminals at rear of inlet valve. Place inner wall assembly lengthways through wall opening and arrange assembly so that metal bracket is flush with inside surface of wall. Screw inlet to wall as described previously in STEP 1, then complete as per (Fig.13) | |
Wall Valve Installation — New ConstructionSelect a probable location for inlet valve and drill a pilot hole in the floor. go below to check that the tubing path is clear of present, or future, obstructions such as floor joists, heating ducts, plumbing, wires, etc. | ![]() | |
![]() | Cut a length of low voltage wiring; bring approximately 6” through the top wire guide hole in stud bracket assembly and double it back into the elbow hole. Tape wire to tubing at assembly elbow and again close to end, and tuck remaining wire into bottom of tubing. Fasten plaster guard onto face of assembly. Drop bottom of tubing through 2 1/4” hole and nail stuff mounting bracket assembly stud. Make sure center of inlet hole is at the correct height above floor level and tubing extends below sub-flooring. Go to STEP 2 installation of tube system and complete tubing system as much as possible. After the walls are finished and painted, the plaster guards will be removed and inlet valves installed. The tubing system may be completed at that time and the power unit installed. | |
STEP 2: Installation of Tube System (New or Existing Home)Tubing System InstallationStarting at the inlet furthest from the power unit, temporarily fasten the main line in position. (Good idea: from a nail or overhead pipe, etc., make two looks of string or low voltage wire to pass PVC tubing through, to hold it in position while you work). Push a length of PVC tubing up in to the bottom of the inlet valve assembly. Bear in mind tube enters all fittings approximately 3/4”. Measure, cut, and slip-fit this vertical line to main horizontal line with a 90° sweep elbow. Remove all inside burrs on end of tubing with pocketknife. Apply cement to both parts and assemble. Connect additional inlet valves to main truck line with 90° “Y” assembly. (Fig.16) | ![]() | |
![]() | Always run branch lines, from sides or top of main trunk line, never out of the bottom as this will create a trap for dirt to fall into. Be sure to install “Y” fittings so sweep | |
The power unit is screwed to the wall with the bottom screws of the mounting bracket about 48” (120 cm) up from the floor to allow convenient removal of the dirt canister. For proper motor cooling there must be at least 8” (20 cm) between the unit and the ceiling. If mounting on plaster or panel walls, ensure mounting bolts enter wall studs. If mounting on concrete walls, 2” x 4” studs or plywood may be suspended from overhead. With the power unit moun ed, strip the low voltage wire and remove the two silver colour “Quick Connect” or “slip-on” terminals from the control panel with a pair of pliers and insert the wire into the “Quick Connect” terminals and crimp and insert the silver ter minals back into place. Note: There are no polarity requirements. | Connect main 2” tubing line to the intake assembly on the power unit (some power units have the optional left or right side intake). Do not cement this last connection to power unit for service and in case you wish to remove at some future date. Teflon tape may be used. The unit may be exhausted to expel odour, very fine dust, germs, and some noise. To reduce noise you could add the optional exhaust muffler. Use same standard pipe and fittings as before. |
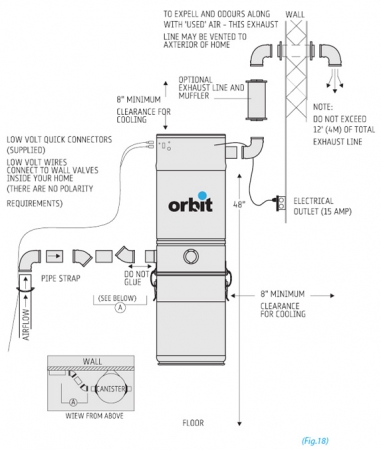